- Home
- Public Employees Occupational Safety and Health
- PEOSH Health Standards
- PEOSH Lead in Construction Standard (29 CFR 1926.62)
PEOSH Lead in Construction Standard (29 CFR 1926.62)
Pure lead (Pb) is a heavy metal (at room temperature and pressure) and is a basic chemical element. It can combine with various other substances to form numerous lead compounds.
When absorbed into the body in certain doses lead is toxic. It can be absorbed into the body by inhalation and ingestion. Except for certain organic lead compounds not covered by this standard, lead is not absorbed significantly through the skin. When scattered through the air as a dust, fume, or mist, lead can be inhaled and absorbed through the lungs and upper respiratory tract. Inhalation of airborne lead is generally the most important source of occupational lead absorption. Lead also can be absorbed through the digestive system if it enters the mouth and is ingested.
A significant portion of the lead inhaled or ingested gets into the blood stream. Once in the blood stream, lead is circulated through the body and stored in various organs and body tissues. Some of this lead is quickly filtered out of the body and excreted, but some remains in the blood and tissues. As exposure continues, the amount stored will increase if the body is absorbing more lead than it is excreting. The lead stored in the tissues can slowly cause irreversible damage, first to individual cells, then to organs and whole body systems.
Lead adversely affects numerous body systems and causes forms of health impairment and disease that arise after periods of exposure as short as days (acute exposure) or as long as several years (chronic overexposure). A short-term dose of lead exposure can lead to acute encephalopathy, a condition affecting the brain that develops quickly into seizures, coma, and death from cardiorespiratory arrest.
Short-term occupational exposures of this type are highly unusual, but not impossible. Similar forms of encephalopathy, however, may arise from extended chronic exposure to lower doses of lead. Consequently, there is no sharp distinction between rapidly developing acute effects of lead and longer term chronic effects.
Damage to the central nervous system in general and the brain in particular is one of the most severe forms of lead poisoning. Chronic overexposure to lead also significantly impairs the reproductive systems of both men and women. Lead can alter the structure of sperm cells - raising the risk of birth defects - and there is evidence of miscarriage and stillbirth in women exposed to lead or whose husbands have been exposed to lead. Children born of parents who were exposed to excess lead levels are more likely to have birth defects, mental behavioral disorders, or to die during the first year of childhood.
This standard aims to reduce the exposure to lead for construction workers. The most significant way to achieve this is by lowering the permissible exposure limit (PEL) from 200 micrograms per cubic meter of air (200 µg/m3) as an 8-hour time weighted average (TWA) to 50 µg/m3).
The PEOSH Lead in Construction standard establishes minimum requirements for the handling of materials containing lead. Public employees who may encounter lead during their work include building maintenance personnel, plumbers, electricians, laborers, painters, and public works employees.
The PEOSH Lead in Construction Standard has been adopted from the U.S. Department of Labor, Construction Lead Standard (29 CFR 1926.62). Information used in this webpage was obtained from federal Occupational Safety and Health Administration publications.
OSHA Lead in Construction Advisor (version 1.0, September 1999). This interactive software is available to provide compliance assistance to employers who engage in activities that involve the use of lead. Guidance provided by this software includes regulatory applicability, conducting an initial determination, using exposure assessment data, evaluating historic exposure data, and other related help.
- What activities are covered by the standard?
- What are the key provisions of the standard?
- What are the requirements for exposure monitoring?
- What medical surveillance needs to be done?
- What information and training is required?
- What compliance methods are in the standard?
- What control methods are in the standard?
- What are the housekeeping requirements?
- What hygiene facilities and practices are required?
- What are the respiratory protection requirements?
- What protective clothing is needed?
- What records need to be kept?
Q: What activities are covered by the standard?
A: This standard applies to all construction work where an employee may be occupationally exposed to lead. All work related to construction, alteration, or repair including painting and decorating is included. Under this standard, construction includes, but is not limited to, the following:
- Demolition or salvage of structures where lead or materials containing lead are present;
- Removal or encapsulation of materials containing lead;
- New construction, alteration, repair, or renovation of structures, substrates, or portions containing lead, or materials containing lead;
- Installation of products containing lead;
- Lead contamination from emergency cleanup;
- Transportation, disposal, storage, or containment of lead or materials containing lead on the site or location at which construction activities are performed; and
- Maintenance operations associated with construction activities described above.
Q: What are the key provisions of the standard?
A:
- Permissible Exposure Limits
- Exposure Monitoring
- Medical Surveillance
- Medical Removal Protection
- Information and Training
- Compliance Program
- Engineering, Work Practice and Administrative Controls
- Housekeeping
- Hygiene Facilities
- Respirators
- Protective Clothing and Equipment
- Record Keeping
The standard establishes maximum limits of exposure to lead for all workers covered, including a permissible exposure limit and action level as follows:
- Permissible Exposure Limit
The permissible exposure limit, or PEL, sets the maximum worker exposure to lead. For example, no employee may be exposed to lead at airborne concentrations greater than 50 µg/m3 averaged over the 8-hour period. - Action Level
An action level is the level at which an employer must begin certain compliance activities outlined in the standard. The action level, regardless of respirator use, for the lead in construction, standard is an airborne concentration of 30 µg/m3 calculated as an 8-hour TWA.
Q: What are the requirements for exposure monitoring?
A: An initial determination of whether employees are exposed to lead at or above the action level and the results of that determination must be made available based on the following:
- Any information, observation, or calculation that indicates employee exposure to lead
- Any previous measurements of airborne lead
- Any employee complaints of symptoms attributable to lead exposure
- Objective data regarding materials, processes, or operations
The employer may discontinue required monitoring when at least two consecutive measurements - taken at least 7 days apart are below the action level.
Monitoring for the initial determination whether employers are exposed at or above the action level may be limited to a representative sample of those employees exposed to the greatest concentrations of airborne lead. Measurements made within the preceding 12 months, which were performed by the same employer and applicable to the same employee tasks, may be used.
The employer must establish and maintain an accurate record documenting the nature and relevancy of previous exposure data. Instead of performing initial monitoring, the employer may rely on objective data that demonstrate that a particular lead-containing material or product does not result in employees exposure at or above the action level when processing, using, or handling.
Until the employer performs an exposure assessment and documents that employees are not exposed above the PEL, the employer must treat employees performing certain operations as if they were exposed above the PEL.
This means providing respiratory protection, protective work clothing and equipment, change areas, hand washing facilities, biological monitoring, and training as required by the standard for the following tasks:
- Manual demolition of structures (e.g., dry wall), manual scraping, manual sanding, and use of heat gun where lead containing coatings or paints are present;
- Abrasive blasting enclosure movement and removal;
- Power tool cleaning
- Lead burning
- Using lead-containing mortar or spray painting with lead-containing paint
- Abrasive blasting, rivet busting, or welding cutting, or burning on any structure where lead-containing coatings or paint are present
- Clean-up activities where dry expendable abrasives are used; and
- Any other task the employer believes may cause exposures in excess of the PEL.
Monitoring and Observing
If the initial determination proves employee exposure is below the action level, further determination need not be repeated unless there is a change in processes or controls.
If employee exposure is at or above the action level, but at or below the PEL, the employer must perform monitoring at least every 6 months and continue until at least two consecutive measurements taken at least 7 days apart are below the action level.
If employee exposure is above the PEL, the employer must perform monitoring quarterly and continue until at least two consecutive measurements taken at least 7 days apart are at or below the PEL but at or above the action level. The employer then must repeat and continue monitoring every 6 months to bring the exposure to or below the action level as described above.
When there has been a change of equipment, process, control, personnel, or a new task has been initiated that could increase employee lead exposure at or above the action level, the employer must conduct additional monitoring.
The employer must notify each employee in writing of employee exposure assessment results within 5 working days after their receipt. Whenever the results indicate that the representative employee exposure, without the use of respirators, is at or above the PEL, the employer must include a written notice stating that the employee's exposure was at or above that level and describe the corrective action taken or to be taken to reduce exposure to below that level.
The employer must provide affected employees or their designated representatives an opportunity to observe any monitoring of employee lead exposure. The employer must provide the observer with and ensure the use of respirators and protective clothing and equipment when monitoring requires entry into an area where they are necessary. The observer, who must comply with all applicable safety and health procedures, is entitled to receive an explanation of the measurement procedures, observe all steps related to lead monitoring performed at the place of exposure, and record the results obtained or receive copies of the results when returned to the laboratory.
Q: What medical surveillance needs to be done?
A: Employers must make available, at no cost to the employee, initial medical surveillance for employees occupationally exposed to lead at or above the above the action level for more than 1 day per year. For employees with exposure more than 30 days per year and who have a blood lead level over 40 µg/dl, full medical surveillance is required.
All medical exams must be performed by or under the supervision of a licensed physician. In addition, full medical examinations with extensive testing must be made available to those employees exposed at or above action level for more than 30 days per year.
Initial medical surveillance must include biological monitoring in the form of blood sampling and analysis for lead or zinc protoporphyrin levels. Biological monitoring tests must be conducted in an OSHA- approved lab and be accurate (to a confidence level of 95 percent) within plus or minus 15 percent, or 6 µg/dl, whichever is greater. The tests must be performed as follows:
- At least every 2 months for the first 6 months and every 6 months thereafter for employees exposed at or above the action level for more than 30 days annually.
- At least every 2 months for employees whose last blood sampling and analysis indicated a blood lead level at or above 40 µg/dl; and
- At least monthly during the removal period for each employee removed from exposure due to an elevated blood lead level.
Within 5 days of receiving biological monitoring results, the employer must notify each employee, in writing, of his/her blood lead levels. Employees whose blood lead levels exceed 50 µg/dl must be removed temporarily with medical removal protection benefits, such as pay, seniority, and other rights.
When the results of a blood lead level test indicate the level exceeds the criteria for medical removal, the employer must provide a second (follow-up) blood sampling test within 2 weeks after receiving initial test results to confirm that removal is necessary.
Under certain limited circumstances, special drugs called chelating agents may be administered to remove circulating blood lead. Using chelation as a preventive measure, that is to lower blood level but continue to expose a worker, is prohibited and therapeutic or diagnostic chelations of lead that are required must be done under the supervision of a licensed physician in a clinical setting. The employee must be notified in writing prior to treatment.
The employer must make available medical exams to employees exposed at or above the action level for more than 30 days per year as follows:
- At least annually for each employee whose blood lead level within the past 12 months was at or above 40 µg/dl;
- When the employee has developed signs or symptoms commonly associated with lead intoxication;
- When the employee is pregnant; and
- When medically appropriate for employees removed from lead exposure due to a sustained health risk or following a final medical determination.
Medical exams must include the following information:
- Detailed work and medical histories, with particular attention to past lead exposure (occupational and non-occupational), personal habits, (smoking and hygiene), and past gastrointestinal, hematologic, renal, cardiovascular, reproductive, and neurological problems;
- A thorough physical exam, with particular attention to gums, teeth, hematologic, gastrointestinal, renal, cardiovascular, and neurological systems; evaluation of lung function if respirators are used;
- A blood pressure measurement;
- A blood sample and analysis to determine blood lead level; hemoglobin and hematocrit determinations, red cell indices, and an exam of peripheral smear morphology; zinc protoporphyrin; blood urea nitrogen; and serum creatinine;
- A routine urinalysis with microscopic exam, and
- Any lab or other test the examining physician deems necessary.
The employer must provide all examining physicians with a copy of the Lead in Construction Standard, a description of the affected employee's duties, the employee's lead exposure level, a description of personal protective equipment used, prior blood lead determinations, and all prior written medical opinions for the employees.
The employee must receive written medical opinions from each examining or consulting physician that contain the following:
- Opinions regarding any detected medical condition that could place the employee at an increased health risk from lead exposure
- Recommendations for special protective measures or limitations on the employee's exposure;
- Limitations on the employee's use of respirators; and
- Results of all prior blood lead determinations
The examining physician must not reveal to the employer either by written or oral opinion any findings unrelated to the employee's occupational exposure to lead. The physician must advise the employee of any medical condition (occupational or non-occupational) that requires further medical attention.
If the employer selects the initial physician to conduct medical exams or consultation, the employee may designate a second physician to review the findings of the first physician and to conduct exams, consultations, and tests as the second physician deems necessary. The employer must promptly notify each employee of the right to seek a second medical opinion following each medical exam or consultation conducted by the initial physician.
- Until the employee (1) informs the employer of his/her intent to seek a second medical opinion and (2) initiates steps to make an appointment with a second physician (within 15 days after receipt of notification or receipt of the initial physician's written opinion), the employer may condition his/her participation in and payment for the multiple physician review mechanism. If the findings of the second physician differ from those of the initial physician, the employee and employer must work together to see that the two physicians resolve any disagreement. If no agreement is feasible, the employer and employee may designate a third physician to review findings and conduct exams, tests, and consultations to resolve the disagreement. The employer must act on the third physician's recommendations unless the employer and employee reach agreement consistent with those of at least one of the three physicians.
Medical Removal Protection
Employers must remove employees with lead exposure at or above the action level each time:
- A periodic and follow-up blood sampling test indicates a blood lead level at or above 50 µg/dl; and
- A final medical determination indicates a detected medical condition that increases health risks from lead exposure.
Employers must return employees to their former job status when:
- Two consecutive blood sampling tests indicate a blood lead level is at or below 40 µg/dl for employees removed due to a blood lead level at or above 50 µg/dl; and
- A subsequent final medical determination indicates there is no longer a detected medical condition that increases health risks from lead exposure.
The employer must remove any limitations placed on employees or end any special protective measures when a subsequent final medical determination indicates they are no longer necessary.
When the multiple physicians' review mechanism has not yet resulted in a final medical determination, the employer must:
- Remove employees from lead exposure, provide special protective measures, or place limitations on employees; or
- Return employees to their former job status; end special protective measures; and remove limitations except when the initial removal, special protection, or limitation resulted from a medical determination different from the finding of the initial physician, or when the employee has been on removal status for the preceding 18 months due to an elevated blood lead level and must await final medical determination.
The employer must provide up to 18 months of medical removal protection benefits each time an employee is removed from lead exposure. As long as the position/job exists, the employer must maintain the earnings, seniority, and other employment rights and benefits as though the employee had not been removed from the lead exposure. The employer may condition medical removal protection benefits on the employee's participation in follow-up medical surveillance.
If a removed employee files a worker's compensation claim for a lead-related disability, the employer must continue medical removal protection benefits pending the disposition of the claim. The employer's obligation will be reduced to the extent that the employee received compensation for earnings lost during removal either from a publicly or employer-funded compensation program or from employment with another employer during the employee's removal.
Q: What information and training is required?
A: The employer must inform employees about lead hazards, including but not limited to warning signs and labels, material safety data sheets (MSDSs), and employee information and training.
For example, the following warning signs must be posted in each work area where employee exposure to lead is above the PEL:
WARNING LEAD WORK AREA POISON NO SMOKING OR EATING |
All signs must be well lit and kept clean so that they are easily visible. Statements that contradict or detract from the signs' meaning are prohibited. Signs required by other statutes, regulations, or ordinances, however, may be posted in addition to, or in combination with this sign.
The employer must institute a training program and ensure participation by all employees subject to exposure to lead or lead compounds at or above the action level on any day. Initial training must be provided prior to initial job assignment or the start-up date for this requirement, whichever comes last. Training must be repeated at least annually and must include the following:
- The content of the standard and its appendices;
- The specific nature of operations that could lead to lead exposure above the action level;
- The purpose, proper selection, fit, use, and limitations of respirators;
- The purpose and a description of the medical surveillance program, and the medical removal protection program;
- The engineering and work practice controls associated with employees'
- The contents of the compliance plan in effect;
- Instructions to employees that chelating agents must not be used routinely to remove lead from their bodies and when necessary only under medical supervision; and
- The right to access records under "Access to Employee Exposure and Medical Records, 29 CFR 1910.20.
All materials relating to the training program and a copy of the standard must be made readily available to all employees.
Q: What compliance methods are in the standard?
A: Prior to each job where employee exposure exceeds the PEL, the employer must establish and implement a written compliance program to reduce employee exposure to the PEL or below. The compliance program must provide for frequent and regular inspections of job sites, materials, and equipment by a competent person. Written programs, which must be revised and updated at least every 6 months, must include the following:
- A description of each activity in which lead is emitted (e.g., equipment used, material involved, controls in place, crew size, employee job responsibilities, operating procedures, and maintenance practices);
- Specific plans to achieve compliance and engineering plans and studies were engineering controls are required;
- Information on the technology considered to meet the PEL;
- Air monitoring data that document the source of lead emissions;
- A detailed schedule for implementing the program, including copies of documentation (e.g., purchase orders for equipment, construction contracts);
- A work practice program including regulations for the use of protective work clothing and equipment and housekeeping and hygiene facility guidelines;
- An administrative control schedule for job rotation, if used;
- A description of arrangements made among contractors on multi-contractor sites to inform affected employees of potential exposure to lead and their responsibility to comply with this standard; and
- Any other relevant information
Q: What control methods are in the standard?
A: The Lead in Construction Standard requires employers to use, when feasible, engineering, work practice, and administrative controls to reduce and maintain employee lead exposure to or below the PEL. When all feasible controls have been instituted but are not sufficient to reduce employee exposure to or below the PEL, they must be used to reduce exposure to the lowest feasible level and supplemented by respirators.
Engineering controls reduce employee exposure in the workplace either by removing or isolating the hazard or isolating the worker from exposure through the use of technology. Under the Lead in Construction Standard, mechanical ventilation may be used to control lead exposure. If used, the employer must evaluate, as necessary, the mechanical performance of the system in controlling exposure to maintain its effectiveness.
Work practice controls reduce the likelihood of exposure by altering the manner in which a task is performed. Safe work practices under the Lead in Construction standard include but are not limited to maintaining separate hygiene facilities (i.e., change rooms, showers, hand washing facilities, and lunch areas) and requiring proper housekeeping practices (i.e., clean-up methods).
Q: What are the housekeeping requirements?
A: All surfaces must be maintained as free a practicable of accumulations of lead. Compressed air must not be used to clean up floors and other surfaces where lead accumulates unless it is used in conjunction with a ventilation system designed to capture the airborne dust created by the compressed air. Shoveling, dry or wet sweeping, and brushing must be used only where vacuuming and other equally effective methods have been tried and found to be ineffective.
Vacuums must be equipped with high-efficiency particulate air (HEPA) filters and used and emptied in a manner that minimizes the reentry of lead into the workplace.
Q: What hygiene facilities and practices are required?
A: Food, beverages, tobacco products, and cosmetics are prohibited in all areas where employees are exposed to lead above the PEL regardless of respirator use.
Employers must provide clean change areas and hand washing and shower facilities, where feasible, for employees who work in areas where airborne exposure to lead is above the PEL regardless of respirator use, or as interim protection (except for showers) for employees performing tasks specified in the "Assessing Exposures" section of this publication. Change areas must be equipped with separate storage facilities for protective work clothing and equipment and for street clothes to prevent cross-contamination.
Shower facilities must contain an adequate supply of cleansing agents and towels for those employees required to shower. Employees required to shower must not leave the workplace wearing any protective clothing or equipment worn during the work shift.
Where showers are not provided by the employer, employees must wash their hands and face at the end of the workshift. The employer must provide adequate handwashing facilities including an adequate supply of water, soap, and clean towels for employees.
Employers also must provide lunchroom facilities or eating areas for employees who work in areas where their airborne exposure to lead is above the PEL regardless of respirator use. These facilities must be as free as practicable from lead contamination and be easily accessible to all employees. Employees must wash their hands and face prior to eating, drinking, smoking or applying cosmetics in eating areas. In addition, employees are prohibited from entering these areas when wearing personal protective clothing or equipment unless surface lead dust has been removed by vacuuming, downdraft booth, or other cleaning method.
Administrative Controls can be used to reduce employee exposure by removing the employee from the hazard (i.e., job rotation). If administrative controls are used to reduce employee exposure to lead, the employer must establish and implement a job rotation schedule. The program must identify by name or number each affected employee; specify the duration and exposure level at each job or work station where each affected employee is located; and include other information useful to assess the reliability of administrative controls to reduce employee lead exposure.
Q: What are the respiratory protection requirements?
A: The employer must provide respiratory protection, at no cost to the employee, and must ensure its use when:
- Employee exposure to lead exceeds the PEL;
- Engineering and work practice controls are not sufficient to reduce exposure levels to or below the PEL;
- An employee requests a respirator; and
- As interim protection for employees performing the tasks listed under the "Assessing Exposures" section of this publication and section (d)(2) of the standard.
An appropriate respirator, which has been approved by the Mine Safety and Health Administration (MSHA) and NIOSH must be selected to protect against lead dust, fumes, and mists. (See the table for recommended respiratory protection).
Respirators issued to employees must exhibit minimum facepiece leakage and fit the employee properly. Employers must perform either quantitative or qualitative (for half-mask respirators only) face fit tests at the time of initial fitting and at least every 6 months for each employee wearing a negative-pressure respirator. If the employee shows signs of breathing difficulty during the fit test or during use, the employer must make available an examination in accordance with the medical surveillance requirements of the standard.
Employees who use filter respirators must be permitted to change the filter elements whenever an increase in breathing resistance is detected and must be allowed to leave work areas to wash their faces and respirator facepieces whenever necessary to prevent skin irritation associated with respirator use.
A respiratory protection program is required in accordance with 29 CFR 1910.134.
Q: What protective clothing is needed?
A: The employer must provide at no cost to the employee and ensure the proper use of personal protective equipment where employees are exposed to lead above the PEL, are exposed to lead compounds that may cause skin or eye irritation, or as interim protection for employees performing tasks specified in the "Assessing Exposures" section of this publication - regardless of respirator use. Appropriate personal protective work clothing and equipment, which prevent contamination of employees and their garments, include but not limited to coveralls or full-body work clothing; gloves, hats, and shoes or disposable coverlets; and face shields, vented goggles, or other appropriate protective equipment that complies with 29 CFR 1910.133.
The employer is required to provide clean and dry protective clothing at least weekly, and daily to employees whose exposure levels regardless of respirator use are above 200 µg/m3 of lead as an 8-hour TWA.
To maintain the effectiveness of the personal protective clothing and equipment, the employer must:
- Clean, launder, or dispose of contaminated protective clothing;
- Repair or replace torn or defective clothing or equipment; and
- Ensure all protective clothing is removed the end of the work shift in change areas provided for that purpose
All contaminated protective clothing and equipment to be cleaned, laundered, disposed of must be placed in a closed container in the change area to prevent dispersion of lead outside the container. Blowing, shaking or otherwise dispersing lead into the air is prohibited for removing lead from contaminated materials. Containers of contaminated personal protective clothing and equipment must be labeled as follows:
CAUTION: CLOTHING CONTAMINATED WITH LEAD. |
The employer also must inform, in writing, any person who cleans or launders the protective clothing or equipment of the potentially harmful effects of lead exposure.
Q: What records need to be kept?
A: The employer must establish and maintain an accurate record of all monitoring and other data used to conduct employee exposure assessments as required by this standard and in accordance with provisions in 29 CFR1910.20. The following must be included in exposure assessment records:
- The dates, number, duration, location, and results of each sample taken, including a description of the sampling procedure used to determine representative employee exposure;
- A description of the sampling and analytical methods used and evidence of their accuracy;
- The type of respiratory protection worn, if any
- The name, social security number, and job classification of the monitored employee and all others whose exposure the measurement represents; and
- Environmental variations that could affect the measurement of employee exposure.
The employer must maintain an accurate record for each employee subject to medical surveillance, including:
- The name, social security number, and description of the employee's duties;
- A copy of the physician's written opinions;
- The results, as supplied to the examining physician, of any airborne exposure monitoring done for the representative employee and all others represented; and
- Any employee medical complaints related to lead exposure.
In addition, the employer must keep or ensure that the examining physician keeps the following medical records:
- A copy of the medical examination results including medical and work history;
- A description of the laboratory procedures and a copy of any guidelines used to interpret the test results; and
- A copy of the results of biological monitoring.
The employer must maintain for at least the duration of employment an accurate record for each employee subject to medical removal, including:
- The name and social security number of the employee;
- The date on each occasion that the employee was removed from current exposure and the corresponding date which the employee was returned to former job status;
- A brief explanation of how each removal was or is being accomplished; and
- A statement about each removal indicating whether the reason for removal was an elevated blood level.
The employer must maintain a record of any objective data relied on to determine initial exposure if it was used in lieu of exposure monitoring for exposure assessment purposes.
The employer must make all records including exposure monitoring, medical removal, and medical records available upon request to affected employees, former employees, and their designated representatives and to the PEOSH for examination and copying in accordance with 29 CFR 1910.20.
When an employer ceases to do business, the successor employer must receive and retain all required records. If no successor is available, these records must be sent to the PEOSH.
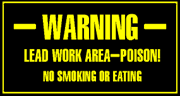
Quick Links
- Search for a Right to Know Hazardous Substance Fact Sheet on lead and lead-containing substances. Available in English and Spanish.
- Lead Training and Certification (permits, contractor licensing)